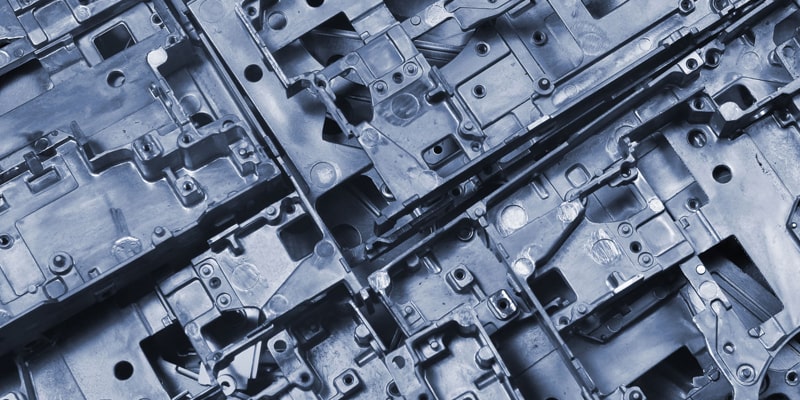
ریخته گری تحت فشار یا دایکاست، از پرکاربرد ترین روشهای تولید انبوه قطعات فلزی پیچیده در صنایع مختلف است. بدین معنی که مواد مذاب تحت فشار به داخل قالب تزریق می شود ریخته گری تحت فشار یا دایکاست نامیده می شود. در این نوع ریخته گری که برخلاف سایر روش ها مواد مذاب به واسطه وزن خود به داخل قالب ریخته می شوند، مواد مذاب با فشار مضاعف به داخل قالب تزریق می شوند. این روش طی فرآیند ذوب، ریختن مواد مذاب به درون قالب (تزریق) و تغییر فاز مواد از مایع به جامد (انجماد) انجام میگیرد. در این نوع ریخته گری امکان تولید محصولات فلزی با وزن بسیار پایین و کیفیت و استحکام بسیار بالا فراهم است. تولید این نوع محصول فلزی با وزن سبک و استحکام بالا در سایر روش های ریخته گری تقریبا غیر ممکن است.
شروع استفاده از این روش به سال ۱۸۲۸ برمی گردد؛ جایی که این ماشین ها اولین بار به منظور استفاده در صنعت چاپ بر سر زبان ها افتادند. در سال ۱۸۴۹ ثبت اختراع این روش صورت گرفت؛ برای ماشین های دستی کوچکی که با هدف استفاده برای چاپ مکانیزه طراحی شده بودند. در نهایت در سال ۱۹۶۶ شرکت جنرال موتورز با بهره گیری از مفاهیم دقت، قابلیت اطمینان و تراکم (منظور همان تولید فشار است) فرایندی به اسم آکوراد (Acurad) را در صنعت دایکاست مطرح کرد.
ریخته گری تحت فشار یکی از کارآمدترین روشهای ساخت قطعات با شکلهای پیچیده، ساختار یکپارچه، ابعاد دقیق، سطح با کیفیت، مقاومت بالا و سختی مناسب است. به همین دلیل، این روش کاربرد گسترده در تولید قطعات تجهیزات صنعتی و کالاهای مصرفی، مخصوصا قطعات اتومبیل دارد. به طور کلی، حدود 60 درصد از قطعات ساخته شده به روش ریخته گری دایکاست در صنعت اتومبیل سازی مورد استفاده قرار میگیرند. این روش در صنایع هوافضا، تجهیزات الکترونیکی، ساخت ماشین آلات صنعتی، ساخت لوازم خانگی، جواهرسازی، مجسمه سازی و غیره کاربرد نیز کاربرد دارد.
یکی از باورهای اشتباه و رایج در خصوص آلمینیوم دایکاست در بازار، پلاستیکی بودن این جنس می باشد؛ در صورتی که این نوع فرایند تولید فقط برای فلزاتی با نقطه ذوب پایین مثل آلومینیوم، مس و... می باشد.
انواع دستگاه دایکاست کدام هستند؟
اجرای فرآیندهای ریخته گری تحت فشار با استفاده از دستگاههای مخصوص انجام میگیرد. به طور کلی، دستگاههای دایکاست به دو نوع دستگاه دایکاست با سیستم تزریق محفظه گرم و دستگاه دایکاست با سیستم تزریق محفظه سرد تقسیم میشوند.
مزایای دایکاست چیست؟
- اشکال پیچیده تری را میتوان تولید کرد.
- نرخ تولید بالا و حداقل نیاز یا عدم نیاز به ماشین کاری
- امکان ساخت قطعات نازک تر نسبت به دیگر روش های ریخته گری و مقاومتر نسبت به روش تزریق پلاستیک (با ابعاد یکسان)
- هزینه پایین نیروی کار
- امکان بازیافت و استفاده مجدد مواد
- قالب های دایکاست مثل قالب های ریژه معمولاً قبل از آنکه فرسوده شوند و در ابعاد قطعه تولید شده اختلافی به وجود آید، هزاران قطعه تولید خواهد کرد، در نتیجه سرمایه گذاری برای تولید قطعه کمتر است.
- خروج راحت تر قطعات به دلیل سطح صاف قالب های دایکاست نسبت به روش های ریخته گری دقیق، ماسهای و دائمی
- تزریق فلزات دیگر و مواد غیر فلزی برای ریخته گری تحت فشار برجا
- مقاومت بالا
- یکپارچگی بالا
- اغلب قطعات تولید شده با کمترین پرداخت، آماده آب فلز کاری هستند.
- قطعات آلومینیومی تولید شده توسط دایکاست معمولاً نسبت به روشهای دیگر مانند ریخته گری آلومینیوم در ماسه مقاومت بیشتری دارند.
با وجود مزایای متعدد ریخته گری تحت فشار، این روش از محدودیتهایی نیز برخوردار است که از مهم ترین آنها عبارت هستند از:
- عدم کاربری مناسب برای فلزات و آلیاژهای دارای نقطه ذوب بالا مانند فولاد
- دشوار بودن قالب گیری و ساخت قطعات بزرگ
- هزینه بالای سرمایه گذاری و تهیه قالب
- زمان نسبتا زیاد چرخه تولید (از دریافت سفارش تا تحویل قطعات به مشتری)
- غیر اقتصادی بودن روش برای تولید قطعات در تعداد کم
مواد مورد استفاده در دایکاست چه هستند؟
ریخته گری تحت فشار معمولا به منظور ساخت قطعاتی از جنس آلیاژهای غیر آهنی مورد استفاده قرار می گیرد. آلیاژهای آلومینیوم، مس، منیزیم و روی از متدوال ترین مواد مورد استفاده در این روش ریخته گری هستند. از این رو، عنوان دایکاست در صنایع مختلف به همراه عبارت مواد مصرفی در آن ها (نظیر دایکاست آلومینیوم یا دایکاست زاماک) شناخته می شود.
تمامی محصولات تولیدی شرکت مهندسی نورفن توسط روش ریخته گری دایکاست؛ دارای استحکام بسیار بالا در برابر ضربه، نور خورشید، آب خوردگی، بارندگی، گرما و سرما و... می باشد.
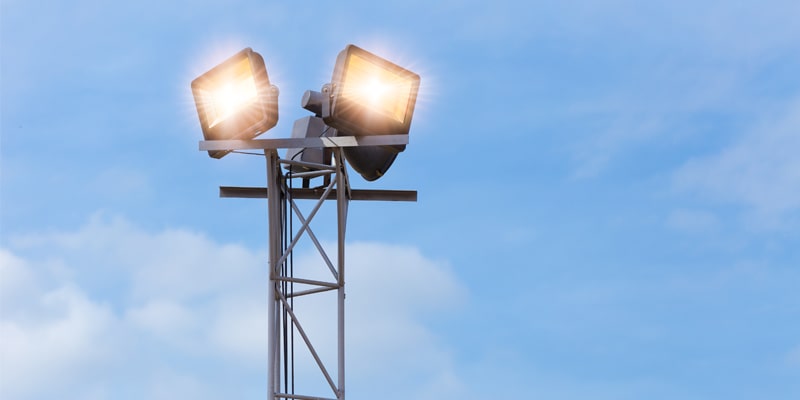
نظرات مشتریان